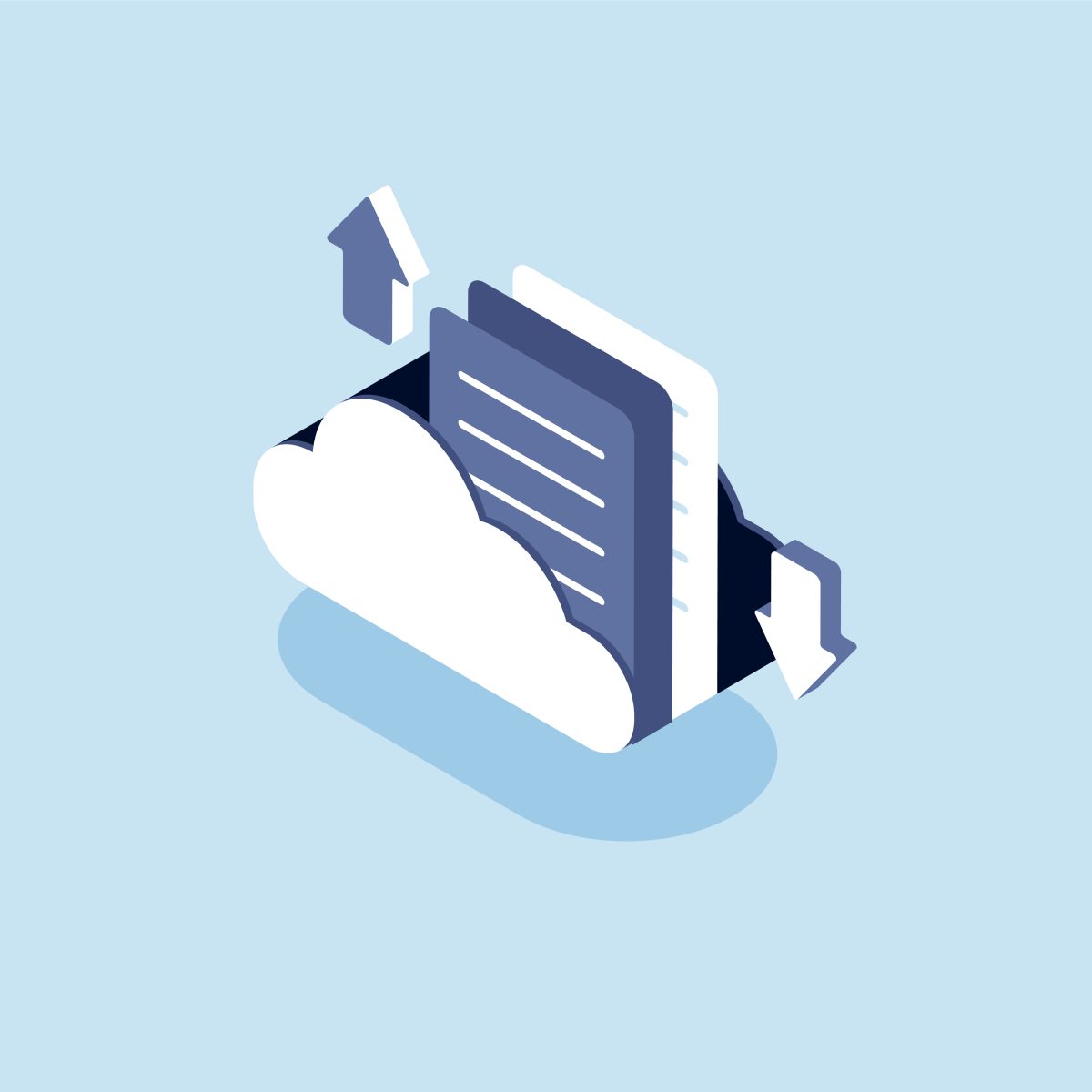
New software version Cmd66_ENU-2.5.0.0.zip of the COMMANDER66 ECU
SECURE METHOD OF ECU UPGRADE
Here is the simple and secure method of update of your ECU with a new software version.
WARNING LEVEL : NORMAL
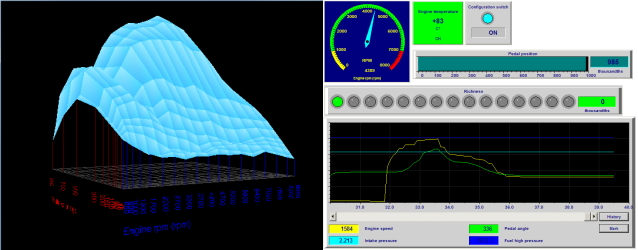
NEW FEATURES AND IMPROVEMENTS
Improvement of sequential gearbox management:
• Optimization of the gear upshift time (faster upshifting).
• Ignition cutoff at gear downshift (faster downshifting on strong brakings of the vehicle).
• Possibility to select the old way of shifting on slower or less precise gearboxes.
• The ECU agrees to intervene on the engine even if the gear position measurement is in error.
Read carefully new documentation for sequential gearboxes.
Improvement of the fly by wires security:
• Stop of the fly by wire electric motor (the throttle closes) when the position measurement potentiometer is in error.
This avoids that the ECU forces on the electric motor, which can cause damages.
CONTENT
Commander66 Tunewares:
• System V240
• Throttle/RPM: V250 (new – 04th 12/2018)
• Pressure/RPM and turbo: V250 (new – 04th 12/2018)
• Archives of all the former Tunewares to open the not yet updated machines of this type
Documentations in English:
• Commander66 tuning software pack: 35 separate documents, each for one specific fonction of the ECU, with many didactic examples (new – 04th 12/2018)
• Commander66 installation: V1.12 – with commands of ignition modules (23rd 06/2015)
• Commander66 options installation: V1.30 – sequential gearboxes, fly by wire, air electrovalves, bang-bang, Vanos BWM … (26th 10/2015)
Nota:
• Does not contain Winjall software. Winjall must first be downloaded and installed apart.
• Does not contain the sensors convertion maps nor the actuators command maps. These maps have to be downloaded and installed apart with the pack SensAct.
LAST SECURITY CRITICAL MODIFICATION DONE
Not needed.
NEEDING Winjall V9.9.0.0 (see specific downloading)
V9.3.0.0 or later version of Winjall software must mandatory have been installed first.
HOW TO UPGRADE TUNEWARES
• Download new .zip Commander66 software pack file and save it in a directory on your hard disk.
• If you have already installed a former version of this pack, you have to usinstall it before installing this new one:
In Windows XP, execute ‘Start/Parameters/Configuration/Add-Remove programs’.
In Windows 7 and latter versions, execute ‘Start/Parameters/Configuration/Programs and features’.
In the software list, select Commander66 then ‘Uninstall’. Follow uninstall instructions.
• With the explorer, double click on the downloaded software pack .zip file, then double click on Setup. At the question on files extraction, answer ‘Extract All’.
• If the installation does not automatically start: in the new directory created by the extraction, double click on Setup (application).
VERSIONS HISTORY
(Improvements are added from a version to the next one)
Papillon/Régime : V240 (Système V230)
Pression/Régime : V240 (Système V230)
1) Improvement of sequential gearbox management:
– A programmable ignition cutoff was already allowed on gear upshift.
– A programmable ignition cutoff has been added on gear downshift, facilitating the gears shifting during difficult conditions.
2) Auxiliary CAN-Bus management:
– Addition of two functions of simplified frames transmission toward the Sybele compatible dashboards.
These functions allow a better confidenciality of the ECU tuning.
Throttle/RPM : V230 (System V230)
Pressure/RPM : V230 (System V230)
1) Securization of the wheels speed measurement:
– In the previous versions, when the wheels speeds were slow, a speed measurement error could happen which was causing a brief dysfunction of the anti skating.
– This version prevents from the speed measurement error.
2) Securization of the engine synchronization with a camshaft target with one supplementary tooth:
– In the previous versions, When the phase sensor was reading a camshaft target with one supplementary tooth, the engine synchronization could fail with an engine start not done.
A second try of engine start was then necessary.
– This version ensures a perfect synchronization of the engine even in these conditions.
3)Improvement of the fuel high pressure control on direct injection engines
The new possibilities of tuning of the high pressure fuel pump in direct injection allow a very improved control of the fuel pressure.
4) Adding of a variable displaying the status of the engine synchronization
This variable gives in real time the engine synchronization and can be recorded with the Winjal scopes to visualize possible problems of synchronization lost causing engine misfires.
Throttle/RPM : V220 (System V220)
Pressure/RPM : V220 (System V220)
1) Significant improvement of the engine startup security:
– In the previous versions, during difficult conditions of engine start-up, the microprocessor could lose the capacity to perform its measurements (throttle, pressures, temperatures, …), causing an engine stalling.
– This version prevents the loss of the measurements even in case of battery tension drop down at the engine start.
2) Very efficient improvement of the launch procedure by a sliding of the launch limiter toward the race limiter:
To avoid the skating at the vehicle take-off, rather than going up suddenty from the launch to the race limiter, the rpm limiter is gradually raised from the launch limiter to the race limiter, at the maximum speed at which you allow the engine to rev up (tunable) – see new limiter documentation.
Throttle/RPM : V210 (System V210)
Pressure/RPM : V210 (System V210)
1) New calibration of the Auxiliary CAN-Bus for new Dashboards:
– A new “Extension” type allows to directly inform the new Dashboards type, like RgCartronic, Gems, Motec, …, and the data recordings devices. With this new type, almost all the measurements and calculation results of the ECU are automatically sent by the Auxiliary CAN-Bus in a simple way.
– This is in addition to the old “Injall” type which allows to directly inform the AIM type Dashboards.
2) Sequential gearbox
– Improvement of the calculation security of the ignition advance modification while gear upshifting: maps of advance modification are not used if “Ignition adavance modification” box is not checked. Whatever is their value, they do not change the ignition advance behavior.
Throttle/RPM : V200 (System V200)
Pressure/RPM : V200 (System V200)
1) Improvement of quality and robustness of the injection command:
– When engine speed instabilities of a sufficient level (due to vibrations or else) happened, the previous versions may lose one or more injections, up to making thinking to a small limiter.
– This new version never loses any injection (nor ignition) whichever is the engine operation.
Throttle/RPM : V190 (System V180)
Pressure/RPM : V190 (System V180)
1) Use of wide band Labda sensors:
– Improvement of the reliability of the injection time self learning at high richness.
– Better detection of Lambda sensor failure.
2) Sequential gearbox
– Automatic boost (autoblip) by the mean of the motorized throttle on gear downshift (needs an analogical powershift switch allowing to detect the downshifting, like strain gauge switches).
– Removal of interventions on injection time on gear upshift – quite never used – (only remains interventions on ignition, used by the whole of the motorists).
– Permission for the user to make the calibration of the gear position potentiometer and of the detection thresholds of the analogical powershift switch, even when the ECU has been locked by a professionnal license.
Throttle/RPM : V170 (System V170)
Pressure/RPM : V170 (System V170)
1) Direct injection:
Modification of injection pressure calculation for gasoline direct injection.
Gives a better adaptation of the injection times to the fuel pressure.
2) Richness correction:
Significant acceleration of richness correction recovery on re-synchronization on exit of rpm sensor signal loss.
Throttle/RPM : V170 (System V170)
Pressure/RPM : V170 (System V170)
1) Sequential gearbox:
More and more gearboxes are equipped with a strain gauge switch, and no more with a On-Off switch.
This version makes much more easier the tuning of this kind of switches.
The new version of the document “sequential gearbox” explains fully how to tune them with this new firmware.
2) RPM sensor signal loss:
Improvement of the resynchronization in case of rpm sensor signal lost.
Throttle/RPM : V160 (System V160)
Pressure/RPM : V160 (System V160)
1) Fuel pressure management:
Improvement of calculations for injection time correction in function of the fuel pressure (see documentation ‘Fuel pressure management’ chapter ‘Fuel pressure reference’).
– The fuel pressure reference, in case of specific calculations for injection time correction in function of the fuel pressure, is now given in pressure relative to atmospheric pressure and no more in absolute pressure.
– If you import the data from an old Tuneware with which the injection time was corrected by the low fuel pressure (not direct injection management), in this old Tuneware, the fuel pressure reference was given in absolute pressure. So you will have to correct the fuel low pressure reference in the new Tuneware.
Throttle/RPM : V150 (System V160)
Pressure/RPM : V150 (System V160)
1) Fly by wire:
– Allows adjusting the detection of a short circuit of the fly by wire.
– Allows the selection between synchronous command mode (standard mode) and asynchronous mode (advised new mode).
The asynchronous mode is preferably to use because
– it allow to manage a more precise position on very small openings, giving a better control of the tick over rpm,
– it consumes less current,
– it makes the electric motor runs cooler,
– it produces less spikes and less noise.
2) Electrical noise:
The interferences filtering on analog inputs have been improved, giving a better stability of the general operation.
Throttle/RPM : V140 (System V150)
Pressure/RPM : V140 (System V150)
1) Ignition:
– Allows the use of coil loading time extremely short (<500 microseconds) for very high efficiency coils or capacitive discharges
– Allows a better load of the coils at engine startup
2) Fly by wire:
– Allowed stop of the fly by wire command below a tuneable rpm, to avoid spikes at the engine start with inductive sensors and save power when the engine does not run
– Allowed stop of the fly by wire command if engine stalls, to avoid spikes with inductive sensors and and allow the automatic cutoff of the fuel pump
Throttle/RPM : V130 (System V140)
Pressure/RPM : V130 (System V140)
1) Injection:
– Self learning of the injection time base map (needs a professionnal license, or on option for standard licenses)
2) Fly by wire:
– Stop of the fly by wire command allowed below a tuneable rpm, to avoid spikes at the engine start with inductive sensors and save power when the engine does not run
3) Camshaft:
– The main camshaft (engine phase) can be the intake or the exhaust one as well
– Reading of camshafts targets with one missing tooth, one supplementary tooth and regular teeth
– Improved responsiveness of Vanos BMW with two electrovalves
Throttle/RPM : V120 (System V120)
Pressure/RPM : V120 (System V120)
Version 120 is the base version of the new Commander66, Skynam high end ECUs.